
Systems Optimization Lab
Department of Mechanical Engineering | McGill University
General research interests
Multidisciplinary design optimization of complex engineering systems; simulation-based engineering design; uncertainty quantification; optimization theory and algorithms; decomposition and coordination methods; design validation; platform-based product families, systems of systems and product-service systems; transportation (automotive and aerospace) and energy systems
Ongoing investigations
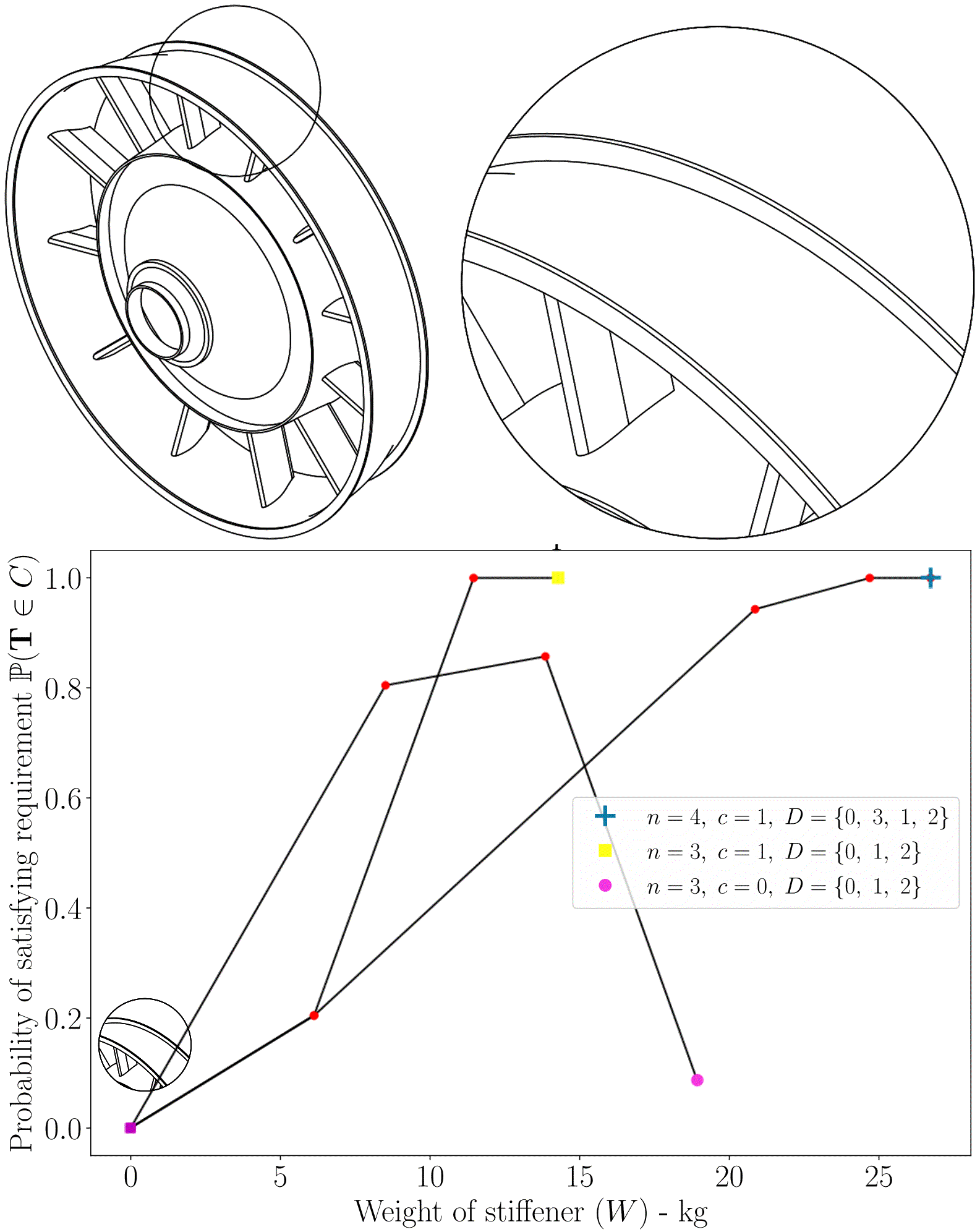
Achieving design scalability by additive manufacturing
The aerospace industry is characterized by a complex supply chain network where design requirements are used to communicate information between original equipment manufacturers (OEM) about feasible design spaces.
While requirements are supposed to be clear and well-defined, they are subject to changes in a product development project. Designers address changing requirements using different design strategies. One strategy involves frequent redesign of the component as system requirements are constantly updated. Frequent redesign is time consuming and costly and should be avoided by managing uncertain requirements. Another strategy for managing change is by building design margins into the component such that it incorporates a buffer against change. This buffer reduces the amount of redesign by absorbing change. This is an example of a robust design. However, incorporating buffer into the component, results in overdesign which may impact product development costs significantly.
A good design strategy is one that minimizes the required changes between component designs without the need for costly overdesign (excessive margins). Novel manufacturing techniques such as additive manufacturing (AM) enable such strategies by allowing ``room for errors'' in the early stages by providing added design scalability. Scalability is defined as the ability of a product to undergo change such that a new requirement level is met.
Finding the optimal scalable design strategy with AM deposition can be a difficult task. We demonstrate this on a turbine rear structure design problem. This component sustains temperature loads as a result of the hot engine exhaust gases. A change in temperature load case requirements can be met swiftly by depositing a stiffener on the outer casing. Excessive material deposition results in overdesign while limited deposition requires significant changes later in the product development cycle. These phenomena are traded against each other in and tradespace exploration strategies using optimization are used to identify the most suitable design strategy.
Contributor: Khalil Alhandawi
Assessing adaptability enabled by additive manufacturing in the design of aeroengine components
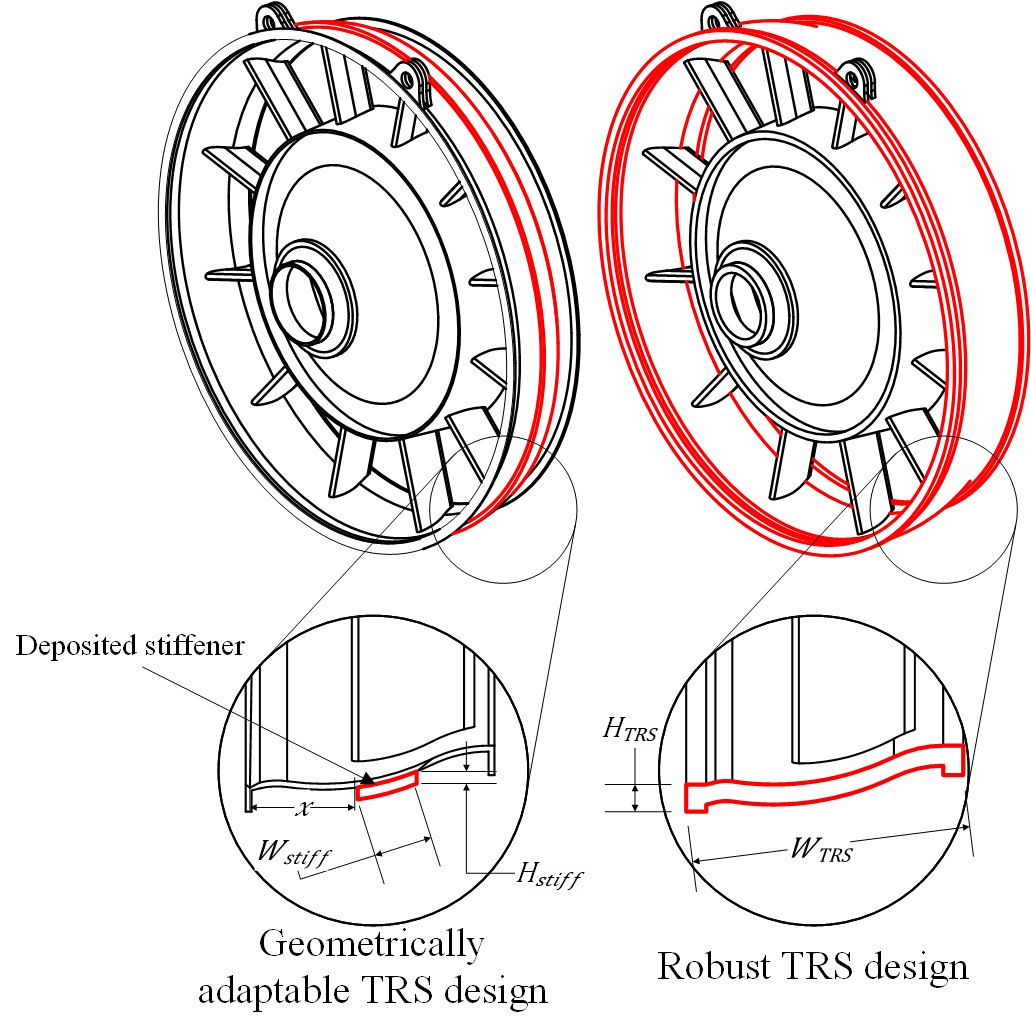
The aerospace industry is characterized by a complex supply chain network where design requirements are used to communicate information between original equipment manufacturers (OEM) about feasible design spaces.
In the aerospace industry, several factors impact components’ lifespan requirements, most of which arise while the airplane is in operation. These uncertain conditions within the industry make it difficult for designers to accurately predict lifespan requirements at the early stages of product development.
Additive manufacturing (AM) is a promising technology for adding a stiffener to a component during operation. This is achieved through the technology’s ability to deposit layers of material on the parent component, resulting in life extension of the component. In this way, products can be designed to have variable lifespan due to their geometric adaptability. Since there are different types of costs associated with robust and adaptable design adoptions, a good design strategy is required to balance the trade-off between robustness and adaptability such that lifecycle cost (LCC) is minimized and performance is maximized.
This research work proposes a dynamic LCC model that estimates total costs over time during the in-service phase. The proposed model is used as a decision-making tool to allow designers to evaluate the use of AM in prolonging the useful life of a component without sacrificing performance and cost. A nested optimization methodology is implemented to integrate component design and lifespan requirement. Results obtained assist designers in selecting an optimum lifespan range to be used as a requirement in early design stages.
Contributor: Lydia Lawand
Artificial Intelligence Aided Aircraft Design and Optimization
Ali is researching the use of artificial intelligence to aid in aircraft design. His investigations can be summarized into two categories:
- Machine learning, such as deep neural networks, application to aid in analysis and reduce computational cost of specific disciplines such as aerodynamics or aircraft performance by acting as surrogate models
- Multi-disciplinary optimization aided by recent advances in the artificial intelligence communities such as sub-set selection or sequential enrichment techniques
Contributor: Ali Tfaily
Analysis automation and optimization for multi-row axial compressor design
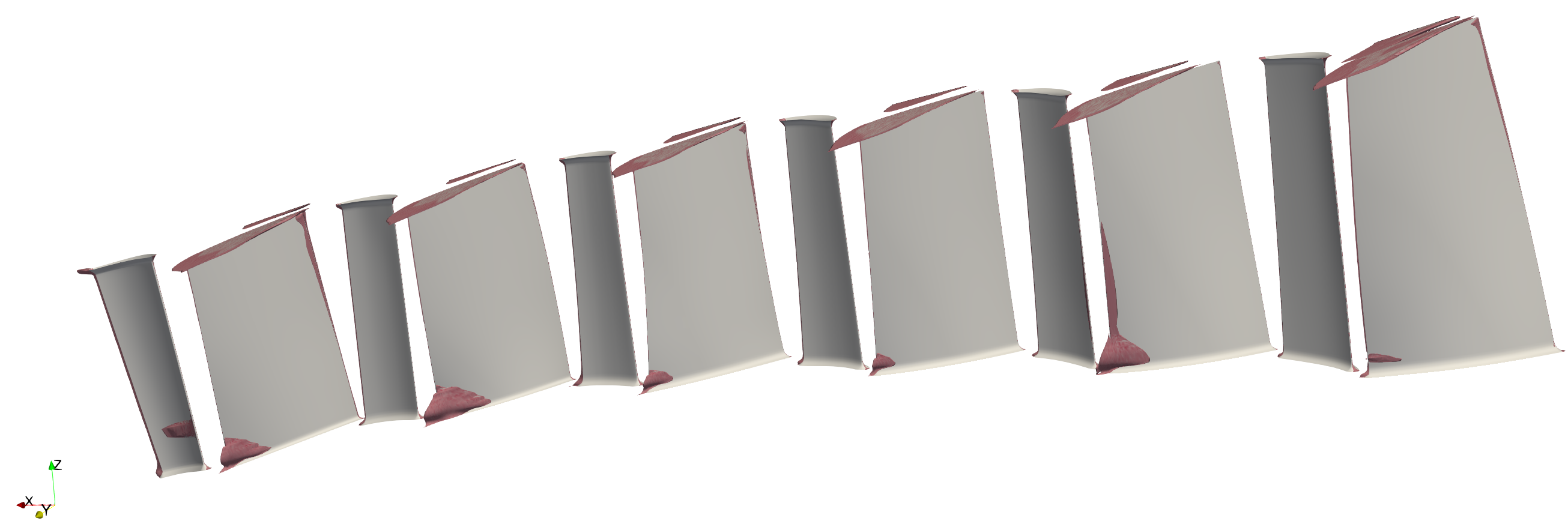
- Axial compressor aero-thermal analysis automation for preliminary airfoil geometry generation for Siemens Energy Aero-derivative Gas Turbines
- Multi-row compressor airfoil geometry parametrization and deformation
- Multi-row compressor airfoil geometry optimization with CFD
- Axial compressor CFD to through-flow matching
- Automation for throughflow driven blade geometry generation
Contributor: Tomas Diaz Jimenez
Completed or currently inactive investigations
Scalable set-based design solutions for product remanufacturing

Engineering design problems involve variable design requirements in the early stages of product development. Set-based design (SBD) is a design paradigm for exploring alternative designs in the early stages of product development and delay commitment to a single design until system requirements are refined. However, even if SBD practices are employed, the designers must commit to a solution eventually. Novel manufacturing technologies allow designs to be remanufacturing to new customer specifications. By considering the capabilities enabled by such technologies during SBD, design solutions can be scaled to meet evolving requirements and customer specifications even after commitment. We developed a SBD methodology that provides scalable design solutions that consider remanufacturing by additive or subtractive manufacturing. The design space is reduced to parametric designs that dominate the requirements space in terms of performance. The set of parametric designs is reduced to scalable designs by observing a set of transition rules for the manufacturing process used. The methodology is demonstrated for a remanufacturing problem in the industry where a structural aeroengine component is reinforced by additive manufacturing deposition to meet higher loading requirements. The results provide a consistent reduction in the design space to yield a set of scalable designs.
Contributors: Khalil Alhandawi, Benjamin Thomsen
Multimodel management in single- and multidisciplinary design optimization
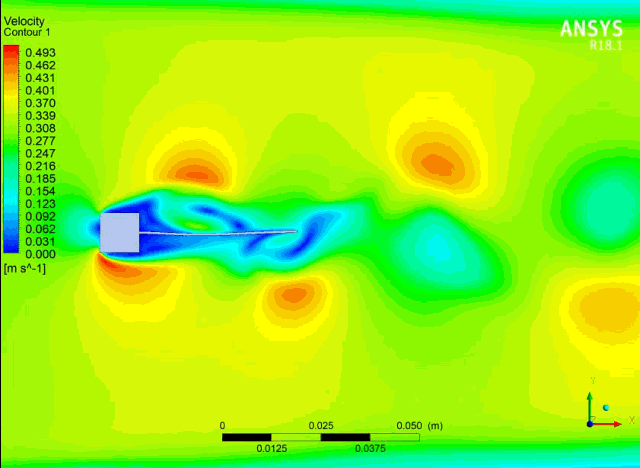
Our research in this area comprises both the development and application of new tools and novel techniques to solve realistic multidisciplinary design optimization (MDO) problems. On the development side, we focus on the development of a relative adequacy framework (RAF) for managing the use of multiple computational analysis models during design space exploration. The goal is to determine whether any of the analysis models associated with lower computational cost (that are typically expected to have inferior predictive capability relative to models associated with higher computational cost) can be used in certain regions of the design space as the latter is being explored during the optimization process. The framework is implemented by means of a set of algorithms for solving single- and MDO problems and is distinguished by the following features:
- Utilizes a rigorous direct search optimization algorithm that does not require gradients or their approximation
- Manages the use of multiple models regardless of their expected fidelity or their disciplinary context by estimating errors and utilizing trust-region principles
- Enables optimization of engineering problems that require expensive computations typically performed by so-called blackboxes
- Applicable to a broad class of time-invariant and time-dependent multidisciplinary design optimization problems
Contributor: Ahmed Bayoumy
Surrogate-assisted, derivative-free optimization for robust simulation-based engineering design

Computer-aided engineering has revolutionized engineering design: computational models are now used to assess alternatives and conduct optimization studies. Challenges of this simulation-based design optimization paradigm include unavailable gradients or unreliable approximations thereof, high computational cost and inherent model uncertainty and noise. Derivative-free optimization (DFO) has been proposed for solving simulation-based design optimization problems. Our work so far has focused on developing a surrogate optimization framework that utilizes i) dynamic regression metamodels to reduce computational cost while handling uncertainty, ii) generalizd pattern search algorithms that have convergence properties and iii) different problem formulations for balancing global vs. local design space exploration and managing lack of information. We have also continued earlier work for conducting appropriate design validation. Our surrogate-assisted strategy exploits the unique features of the Mesh Adaptive Direct Search (MADS) algorithm, and emphasizes the use of surrogate models for acquiring information cost-effectrively while making decisions using the "true" models. Future research aims at developing robust optimization methods for minimizing the sensitivity of DFO design solutions with respect to uncertainties in design variables or model parameters.
Contributor: Bastien Talgorn

Optimization methods for enhanced nanoparticle-based cancer treatment
Our research focuses on three specific topics:
- Design optimization of drug-carrying nanoparticles for minimal toxicity and maximal tumor regression
- Development of dual nanoparticles delivery strategies to overcome the tumors physical barriers and increase nanotherapy efficacy
- Uncertainty quantification of the tumor microenviroment to design robust targeted drug delivery micro- and nano-systems
Contributor: Ibrahim Chamseddine
Multidisciplinary design optimization of engineering systems and systems-of-systems
The motivation for this research is that engineering systems are becoming increasingly complex. In addition, challenging engineering problems may not be solvable by means of monolithic systems; novel design solutions that combine different systems together into systems-of-systems may be required to achieve functionalities that none of the individual systems can provide by themselves. It is widely accepted that the single most important cause of failures or unexpected system behavior is the inability to capture and understand all the interactions that exist among subsystems. This phenomenon is amplified when considering the integration of heterogeneous systems because synergy modes and common objectives are not well understood or defined. Our former research aimed at addressing the interaction and heterogeneity issues by developing hybrid methods for their coordination. In more recent work, we have applied both MDO and bio-inspired methods to air transportation design in the context of systems-of-systems. We have also conducted extensive numerical investigations of hon-hierarchical coordination methods and proposed a novel method for their implementation.
Future research could focus on dynamic and uncertainty aspects: the collective design objectives of the cooperative systems may be either unknown or vaguely defined at the individual system design stages, and they may change over time, especially in the operating phase.
Contributors: Gautam Marwaha, Ibrahim Chamseddine
Modeling and optimization of aerospace product-service systems

A product-service system (PSS) is a commodity overarching goods and services. An aerospace engineering example is a jet engine manufacturing selling propulsion power to an aircraft operator instead of the engine itself. PSSs are viewed increasingly as an attractive means to create additional revenue streams for manufacturers, add value to consumers and contribute to sustainability since life-cycle analysis and management is extremely important to their design, production and use. While the PSS concept is not new (utility companies sell power, vehicle manufacturers offer services such as extended warranties, etc.), the related engineering design literature is very limited. In recent years, this research area has attracted a lot of interest in the engineering design communities of Northern Europe, Korea and Japan, but not in North America. The majority of the literature is qualitative in nature, so our research aims at developing quantitative methods for model-based design optimization of PSSs. Specifically, we are developing methods to generate and assess PSS design alternatives by combining quantitative and qualitative techniques such as Quality Function Deployment (QFD), Value Engineering (VE) and Multidisciplinary Design Optimization (MDO) to identify critical PSS design variables and attributes, model the relationship between them and maximize added value of product-service offerings.
Contributor: Cássio Gonçalves
Integrating air systems in aircraft multidisciplinary design optimization

The complex nature of interaction between aircraft design and air systems design makes it a good candidate for integration into aircraft multidisciplinary design optimization (MDO). This research focuses on investigating methods to capture the sensitivities of air systems design on aircraft design. Air systems that are included in this research are environmental controls systems, ice protection systems, and fuel tank inerting systems. These systems consume pressurized bleed air from an aircraft’s engines to perform their respective functions. We are exploring methods to model the behavior of these systems, which are then incorporated into an MDO environment. This research investigates different techniques to integrate the developed models within the aircraft optimization loop where the interaction and sequencing with engine and wing design models can significantly vary the impact on the overall aircraft design. In addition, we are exploring methods for optimal engine bleed-port selection.
Contributor: Ali Tfaily
Composite stacking sequence optimization using mesh adaptive direct search


The use of composites has been increasing in land, aerospace, and marine applications due to their advantages over conventional isotropic materials. Most importantly, they provide the flexibility to tailor their properties by changing fiber orientation in the material. However, as advantageous as it may seem, this makes the design of laminated composite structures much more complex and tedious due to the large number of design variables (fiber orientation angles). This offers an opportunity to use optimization techniques to design the best suited structure as per the requirements of the specific application. The composite design guidelines and the manufacturing constraints limits the choice of ply orientation angles in a laminate to a set of discrete angles such as, [0◦, ±45◦, 90◦]. Moreover, the complexity exists because of the multi-modal and variable-dimensional design space with unattainable or costly derivatives. For instance, in engineering design optimization, the objective and constraint functions are often evaluated using black-box simulations and cannot be explicitly expressed analytically nor explicitly. Furthermore, it may be inappropriate to estimate the gradients due to costly evaluations and/or inherent noise in the model. This restricts the use of gradient-based optimization methods to solve such design problems. We use the Mesh Adaptive Direct Search (MADS) algorithm, and compare it to the Real-Coded Genetic Algorithm (RCGA) to optimize the helicopter rotor composite box-beam to achieve desired stiffness requirements determined from the aero-elastic analysis. The objective is to compare MADS, which has a proven convergence to the second-order stationary points, with RCGA, which generates solutions according to an arbitrarily chosen termination criterion and whose optimality cannot be characterized.
Contributor: Ashutosh Bhujbal
Multidisciplinary design optimization of vascular stents

Vascular stents are tubular structures which are expanded inside an artery to provide structural support and to restore blood flow. Despite having a huge variety of stents in today's market, the adverse biological responses after stenting have not been completely addressed. In-stent restenosis, for instance, is a major problem of current stents. While the causes of restenosis are not completely understood, several studies have shown that low shear stress at the arterial wall is one of the culprits.
We developed a model for multidiscplinary (structural mechanics and fluid dynamics) design optimization of a vascular stent aiming at addressing these issues. A stent can be essentially considered a planar structure when unfolded. Modelling a stent as a lattice structure enables specific stent properties to be tailored by controlling the topology of the unit cell.
The main structural properties to consider in stent design are: radial strength, flexibility, foreshortening and recoil. The model will also take into account the blood flow around the stent struts because the presence of the stent disturbs the flow and can create regions of low wall shear stress (critically low wall shear stresses can result in hyperplasia causing in-stent restenosis). These stent requirements were addressed by formulating and solving a multi-objective optimization problem. This approach generated a set of Pareto-optimal stent designs that can support medical doctors in making informed decision when choosing a stent.
Contributor: Purnendu Prithipaul